Sand Casting Process Overview
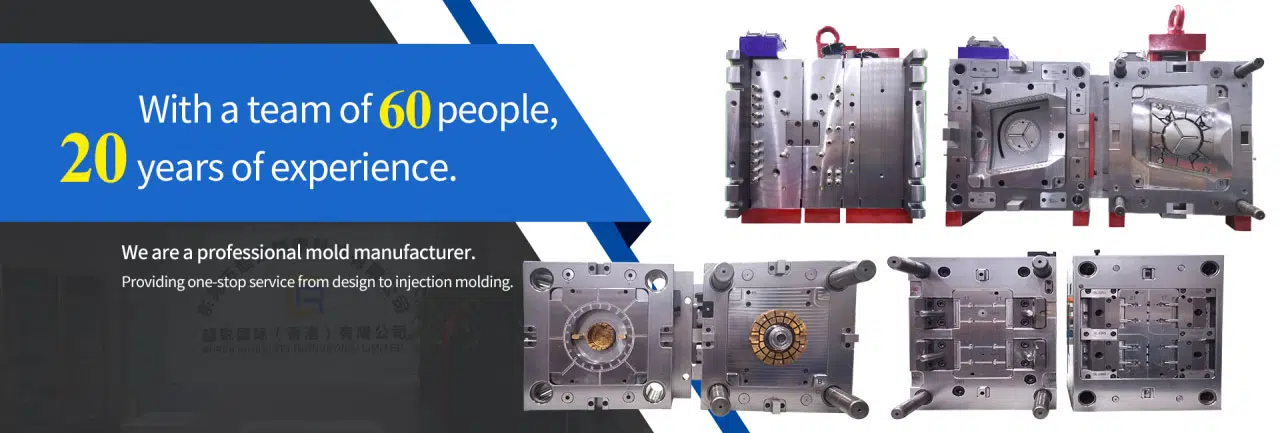
# Sand Casting Process Overview
## Introduction to Sand Casting
Sand casting is one of the oldest and most widely used metal casting processes. This versatile manufacturing method involves pouring molten metal into a sand mold cavity, where it solidifies to form the desired shape. The process is particularly valued for its ability to produce complex geometries in both small and large quantities.
## Key Components of Sand Casting
### 1. Pattern Creation
The process begins with creating a pattern, typically made from wood, plastic, or metal. This pattern represents the final product and is used to form the mold cavity.
### 2. Mold Preparation
A mixture of sand and binder is packed around the pattern to create the mold. The mold consists of two halves:
– Cope (upper half)
– Drag (lower half)
### 3. Core Making (if needed)
For parts with internal cavities, sand cores are created separately and placed in the mold before pouring.
## The Sand Casting Process Steps
1. **Pattern Placement**: The pattern is placed in the drag portion of the flask.
2. **Sand Packing**: Sand is packed around the pattern to form the mold.
3. **Pattern Removal**: The pattern is carefully removed, leaving the cavity.
4. **Core Insertion**: If required, cores are placed in the mold.
5. **Mold Assembly**: The cope is placed on top of the drag.
6. **Metal Pouring**: Molten metal is poured into the mold cavity.
7. **Cooling**: The metal is allowed to solidify.
8. **Shakeout**: The sand mold is broken away from the casting.
9. **Finishing**: Excess material is removed and surface finishing is performed.
## Advantages of Sand Casting
– Cost-effective for small to medium production runs
– Capable of producing large parts
– Wide range of compatible metals (ferrous and non-ferrous)
– Relatively simple tooling requirements
Keyword: Sand Casting
– Good dimensional accuracy for most applications
## Common Applications
Sand casting is used across various industries for producing:
– Engine blocks and cylinder heads
– Pump housings
– Valves and fittings
– Large machine components
– Artistic sculptures and decorative pieces
## Conclusion
Sand casting remains a fundamental manufacturing process due to its flexibility, cost-effectiveness, and ability to produce complex shapes. While newer casting methods have emerged, sand casting continues to be the preferred choice for many applications where these characteristics are essential.