Sand Casting Process Overview
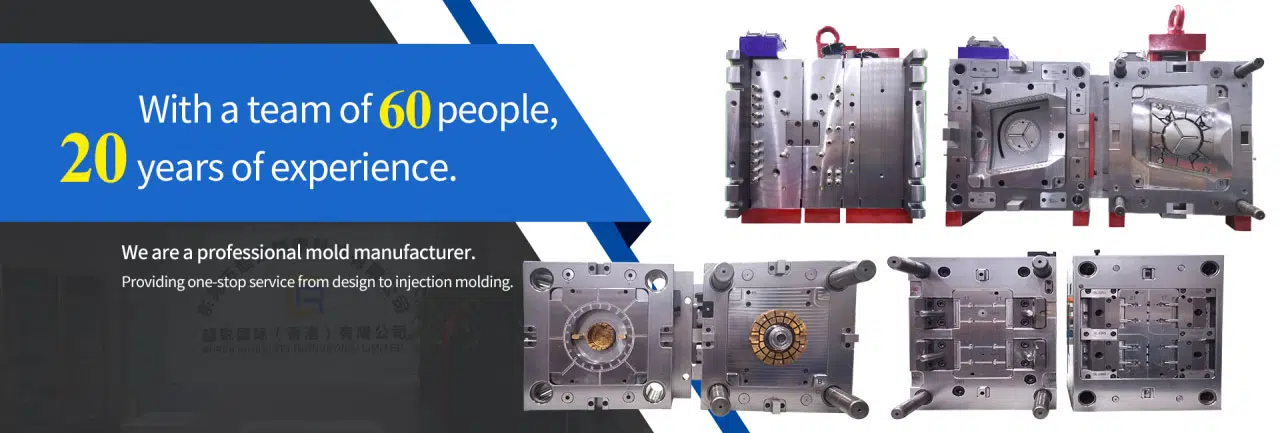
# Sand Casting Process Overview
## Introduction to Sand Casting
Sand casting is one of the oldest and most widely used metal casting processes. This versatile method has been employed for centuries to create complex metal parts with relatively simple equipment. The process involves pouring molten metal into a sand mold cavity, allowing it to solidify, and then breaking away the sand mold to reveal the finished casting.
## The Basic Steps of Sand Casting
### 1. Pattern Creation
The process begins with creating a pattern, which is a replica of the final product. Patterns can be made from wood, metal, plastic, or other materials. The pattern includes allowances for shrinkage and machining.
### 2. Mold Preparation
Molding sand is packed around the pattern in a flask (a metal frame). The sand mixture typically contains silica sand, clay, and water to provide proper bonding and strength. The mold is then carefully separated to remove the pattern, leaving a cavity in the shape of the desired part.
### 3. Core Making (if needed)
For parts with internal cavities or complex geometries, sand cores are created separately and placed in the mold before pouring. These cores are made from special sand mixtures that hold their shape during pouring.
### 4. Mold Assembly
The cope (top half) and drag (bottom half) of the mold are assembled with any necessary cores in place. The two halves are clamped together to prevent leakage of molten metal.
### 5. Pouring
Molten metal is poured into the mold through a sprue (funnel-shaped opening). The metal flows through runners and gates to fill the mold cavity completely.
### 6. Cooling
The casting is allowed to cool and solidify within the mold. Cooling time depends on the metal used and the size of the casting.
### 7. Shakeout
Keyword: Sand Casting
Once cooled, the sand mold is broken apart to remove the casting. This process is called shakeout.
### 8. Finishing
The casting undergoes various finishing operations such as cutting off excess metal (gates and risers), grinding, sandblasting, and sometimes heat treatment or machining to achieve final dimensions.
## Advantages of Sand Casting
Sand casting offers several significant benefits:
– Cost-effective for small to medium production runs
– Capable of producing very large parts (up to several tons)
– Works with nearly all metal alloys
– Allows for complex geometries
– Relatively simple tooling requirements
– Quick turnaround for prototype development
## Common Applications
Sand castings are used in numerous industries including:
– Automotive (engine blocks, cylinder heads)
– Aerospace (turbine housings)
– Construction (pipe fittings, valves)
– Agriculture (equipment components)
– Art and sculpture
## Materials Used in Sand Casting
Nearly any metal that can be melted can be sand cast, but the most common include:
– Cast iron
– Aluminum alloys
– Steel
– Bronze
– Brass
– Magnesium alloys
## Modern Developments
While the basic principles remain unchanged, modern sand casting has seen improvements in:
– Automated molding machines
– Better sand reclamation systems
– Improved binder systems
– Computer simulation of mold filling and solidification
– 3D printed sand molds
Sand casting continues to be a vital manufacturing process due to its flexibility, cost-effectiveness, and ability to produce high-quality metal components across a wide range of industries and applications.